Dosierpumpe für das SNCR-Verfahren
Selektive nichtkatalytische Reduktion von Stickoxiden (SNCR-Verfahren)
VANE-MAG® MPA – korrosionsbeständige und magnetgekuppelte Drehschieberpumpen aus Edelstahl zur Förderung von Ammoniakwasser, technisch dicht nach TA-Luft
Das SNCR-Verfahren ist ein etabliertes Verfahren zur Reduktion von Stickoxiden (NOx) in Abgasen aus Industrieanlagen, wie zum Beispiel Kraftwerken, Zementfabriken oder Müllverbrennungsanlagen. Es ist eine kosteneffektive Möglichkeit, die Emissionen von Stickoxiden und damit die Luftverschmutzung und den sauren Regen zu reduzieren.
Das SNCR-Verfahren basiert auf der Reduktion von Stickoxiden mit Ammoniak (NH3) oder Harnstoff (NH2CONH2) als Reduktionsmittel. Die Reduktion findet bei hohen Temperaturen statt, typischerweise bei Temperaturen von 850-1100 °C. Das Reduktionsmittel wird direkt in den Abgasstrom eingespritzt, bevor die Abgase in den Rauchgasreiniger gelangen.
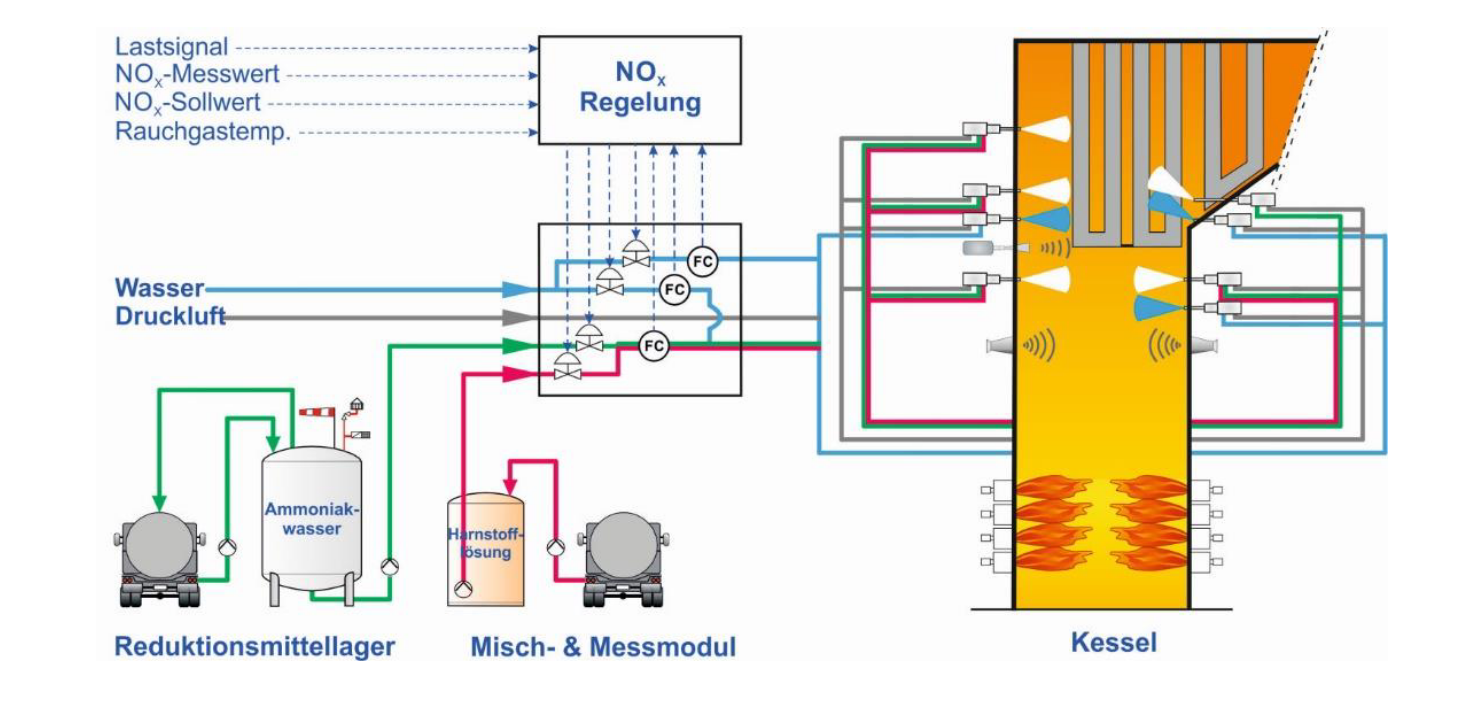
Im Rauchgasreiniger reagiert das Reduktionsmittel mit den Stickoxiden und reduziert sie in Stickstoff und Wasser. Die Reduktion findet statt, indem das Reduktionsmittel mit den Stickoxiden reagiert und die Stickoxide in molekularen Stickstoff und Wasser umwandelt. Der genaue Mechanismus der Reaktion hängt von der Art des Reduktionsmittels, der Temperatur und anderen Faktoren ab.
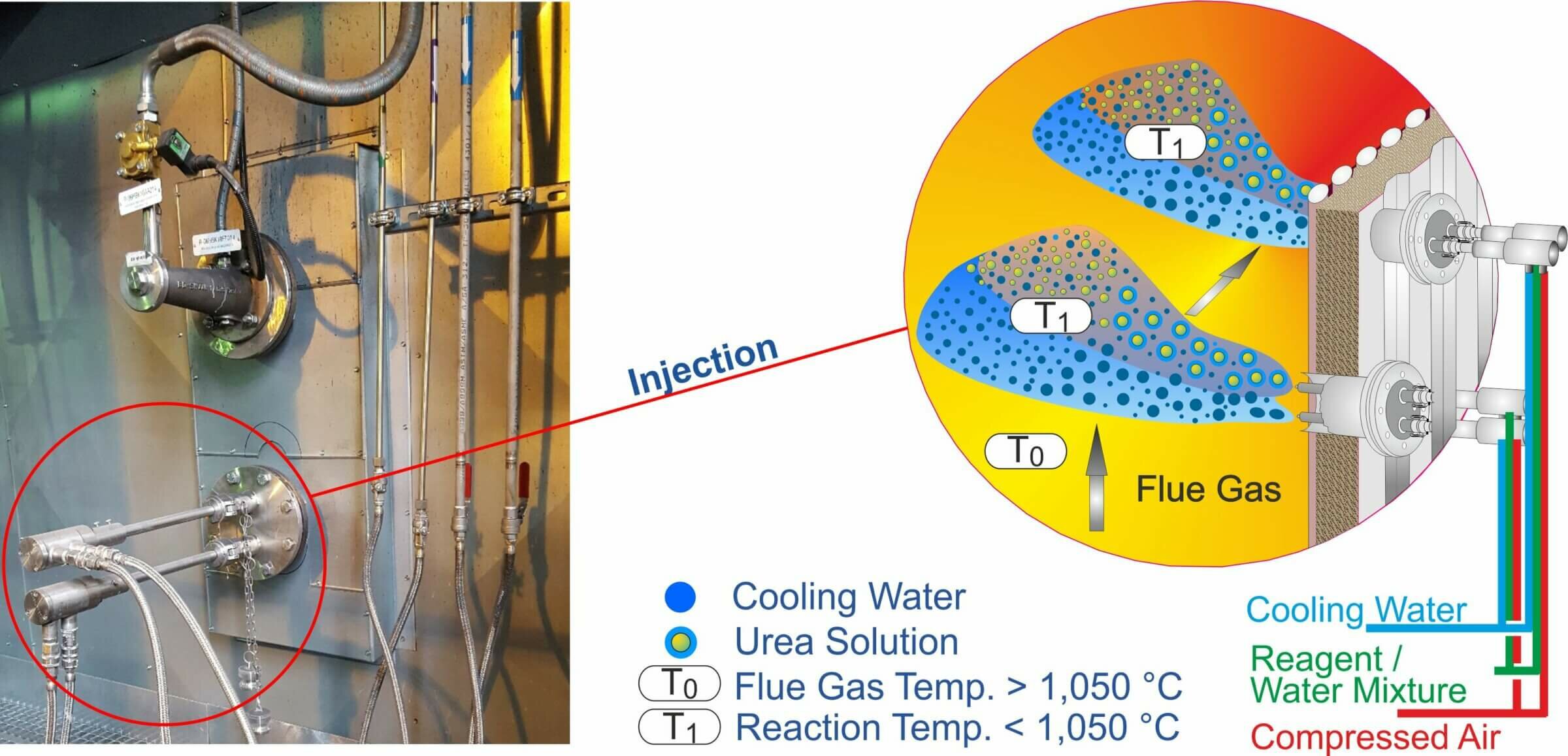
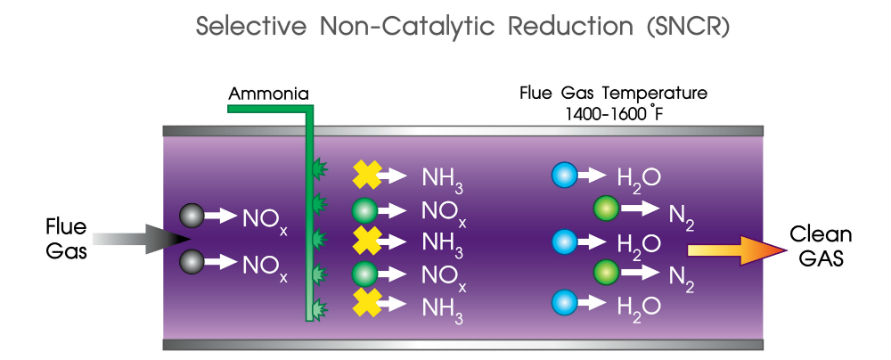
Das SNCR-Verfahren ist selektiv, da es nur auf Stickoxide reagiert, während andere Verbindungen im Abgas wie Schwefeloxide (SOx) und Kohlenmonoxid (CO) nicht beeinflusst werden. Das Verfahren ist auch nicht katalytisch, da es ohne den Einsatz von Katalysatoren auskommt.
Das SNCR-Verfahren hat einige Vorteile gegenüber anderen Abgasreinigungstechnologien, wie zum Beispiel der selektiven katalytischen Reduktion (SCR). Es ist kosteneffektiver als die SCR-Technologie, da es keine Katalysatoren benötigt. Es kann auch in bestehende Anlagen eingebaut werden, ohne dass große Änderungen an der Anlage vorgenommen werden müssen.
Allerdings hat das SNCR-Verfahren auch einige Nachteile. Es hat eine geringere Stickoxid-Reduktionsrate als die SCR-Technologie und ist weniger effektiv bei der Reduktion von Stickoxiden bei niedrigeren Temperaturen. Es ist auch empfindlich gegenüber Änderungen der Betriebsbedingungen, wie z.B. Schwankungen in der Abgaszusammensetzung, der Abgastemperatur und des Luftverhältnisses.
Insgesamt ist das SNCR-Verfahren eine bewährte und kosteneffektive Methode zur Reduktion von Stickoxiden in Abgasen aus Industrieanlagen. Es wird oft in Kombination mit anderen Abgasreinigungstechnologien eingesetzt, um die Emissionen von Schadstoffen in der Luft zu reduzieren und die Luftqualität zu verbessern.
Seit mehr als 20 Jahren beliefern wir den Marktführer im Bereich SNCR-Anlagen, Mehldau & Steinfath Umwelttechnik GmbH und haben in dieser langjährigen Geschäftsbeziehung weit mehr als 200 SNCR-Anlagen mit unseren Gleitschieberpumpen erfolgreich ausgerüstet. Herr Daniel von der Heide steht als kompetenter Ansprechpartner bei Mehldau & Steinfath Umwelttechnik GmbH zu Ihrer Verfügung.
Pumpenauslegung
Für das SNCR-Verfahren werden in der Regel Dosierpumpen eingesetzt, da sie eine präzise Dosierung des Reduktionsmittels ermöglichen. Für die Einbringung des Reduktionsmittels in die Verbrennungsanlage wird ein Differenzdruck von bis zu 10 bar benötigt. Das erforderliche Fördervolumen variiert je nach Größe der Feuerungsanlage, in der Regel werden in Industrieanlagen Volumenströme zwischen 100 und 1000 l/h benötigt. Bei Verwendung von Ammoniakwasser ist es empfehlenswert, eine niedrige Motordrehzahl anzustreben, um den NPSHR zu reduzieren und Kavitation zu vermeiden. Die Wahl zwischen der Verwendung von Frequenzumrichtern oder Überströmventilen zur Dosierung der erforderlichen Menge des Reduktionsmittels in den Verbrennungsraum liegt beim jeweiligen Anlagenbauer.
Die MARCH VANE-MAG® MPA Pumpenreihe hat den Vorteil, dass die Hydraulik selbst besonders effektiv ist. Diese rotierenden Verdrängerpumpen, auch als Drehschieberpumpen bekannt, werden typischerweise eingesetzt, um Flüssigkeiten mit geringer Schmierwirkung zu fördern oder genau zu dosieren. Der Rotor der Pumpe ist mit Nuten versehen, in denen sich die Schieber radial bewegen und gegen die Innenwand der Statorbohrung oder des Hubrings drücken. Auf diese Weise wird bei der Rotation des Rotors ein sich verengender Raum zwischen Schieber und Stator erzeugt, der das Medium ansaugt. Wenn der Schieber weiterbewegt wird, wird das Medium zwischen Schieber und Gehäuse eingeschlossen und durch die Rotation des Rotors zum Auslass der Pumpe befördert. Die Schieber, der Stator und das Axiallager bestehen aus Kohlegraphit und weisen sehr gute selbstschmierende Eigenschaften auf. Zudem sind die Pumpen der Baureihe VANE-MAG® MPA magnetgekuppelt und deshalb hermetisch dicht und Leckagefrei.
Drehschieberpumpen werden oft in Anwendungen eingesetzt, bei denen eine pulsationsfreie und kontinuierliche Förderung von kleinstmengen bei einem hohen Gegendruck erforderlich ist, wie z.B. in der Chemie-, Lebensmittel- und Pharmaindustrie. Sie sind wartungsfrei und haben eine lange Lebensdauer, da sie aus wenigen Teilen bestehen, die bei idealen Betriebsbedingungen nicht leicht verschleißen.
Bildmaterial
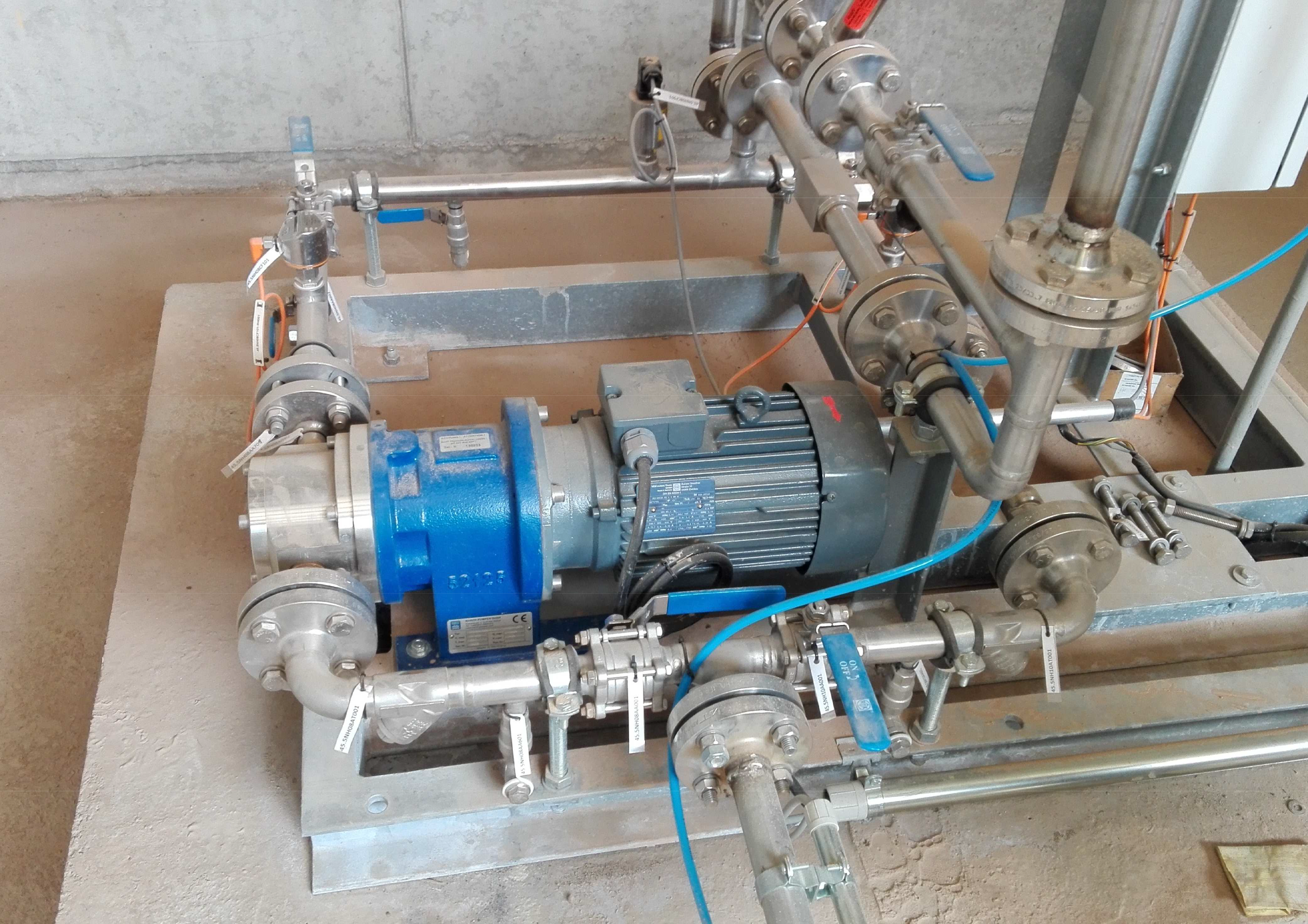