Dosierpumpe für Salzsäure
Herstellung von Biodiesel (Fettsäuremethylester)
VANE-MAG® MP/MPA - korrosionsbeständige und magnetgekuppelte Drehschieberpumpen aus Edelstahl oder Kunststoff zur Förderung von Biodiesel oder Katalysatoren.
TEF-MAG® - korrosionsbeständige und magnetgekuppelte Zahnradpumpe aus Kunststoff zur Förderung von Biodiesel oder Katalysatoren.
MARCH Dosierpumpen der Serien TEF-MAG® und VANE-MAG® sind weltweit in Biodieselanlagen von AirLiquide, ehemals Lurgi AG, und JJ-Lurgi Engineering zu finden. Biodiesel wird aus tierischen oder pflanzlichen Fetten und Ölen hergestellt. Der Prozess der Herstellung von Biodiesel wird als Transesterifikation bezeichnet, bei der die Triglyceride in den Fetten und Ölen durch die Reaktion mit einem Alkohol und einem Katalysator in Biodiesel (Fettsäurealkylester) und Glycerin umgewandelt werden. Die häufigsten Alkohole, die bei der Transesterifikation verwendet werden, sind Methanol oder Ethanol. Der Katalysator kann entweder ein basischer Katalysator wie Natrium- oder Kaliumhydroxid oder ein saurer Katalysator wie Salzsäure oder Schwefelsäure sein.
Der Prozess der Herstellung von Biodiesel besteht aus mehreren Schritten. Zunächst werden die Fettsäuren von den Ölen oder Fetten durch die Zugabe von Natronlauge getrennt. Anschließend wird der Alkohol (z.B. Methanol) mit dem Katalysator gemischt und dann in das Öl eingebracht. Während der Reaktion wird das Glycerin abgeschieden und als Nebenprodukt gesammelt. Der Biodiesel wird von dem restlichen Alkohol und Katalysator durch Waschen mit Wasser getrennt und gereinigt. Der resultierende Biodiesel kann dann als Kraftstoff in Dieselmotoren verwendet werden.
Pumpenauslegung
Für das Eindüsen des Katalysators in den Reaktor werden in der Regel Dosierpumpen eingesetzt, da sie eine präzise Dosierung des Katalysators ermöglichen. Für die Eindüsung des Katalysators in den Reaktor wird ein Differenzdruck von bis zu 10 bar benötigt. Das erforderliche Fördervolumen variiert je nach Größe der Biodieselanlage. In der Regel werden in größeren Industrieanlagen Volumenströme zwischen 50 und 1000 l/h benötigt.
Die Serie VANE-MAG® sowie TEF-MAG® von MARCH PUMPEN vereint hierbei die gute Dosierfähigkeit von rotierenden Verdrängerpumpen, die chemische Beständigkeit durch den Einsatz von komplett nicht-metallischen Materialien, als auch die Leckagefreiheit durch den Einsatz der Magnetkupplungstechnologie. Alle Pumpen dieser Serien sind zudem voll elektrisch leitfähig nach ATEX 2014/34/EU für die ATEX Zone 1 und / oder 2 lieferbar.
Bildmaterial
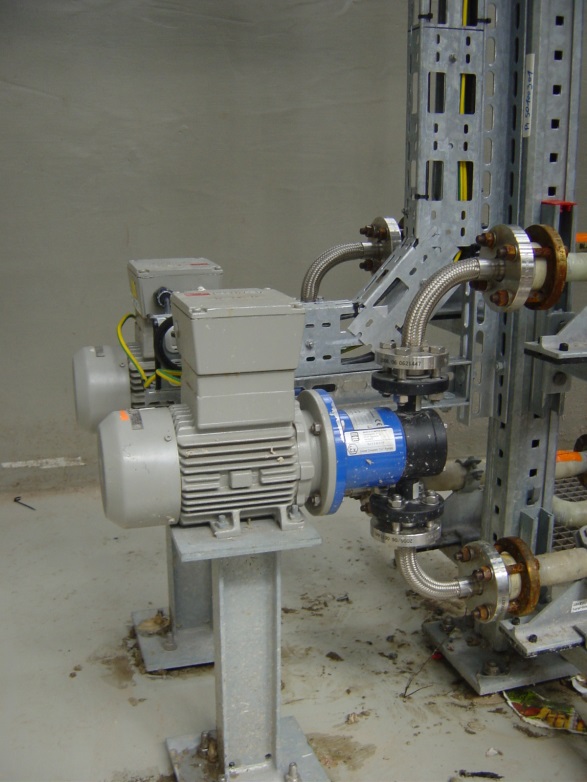
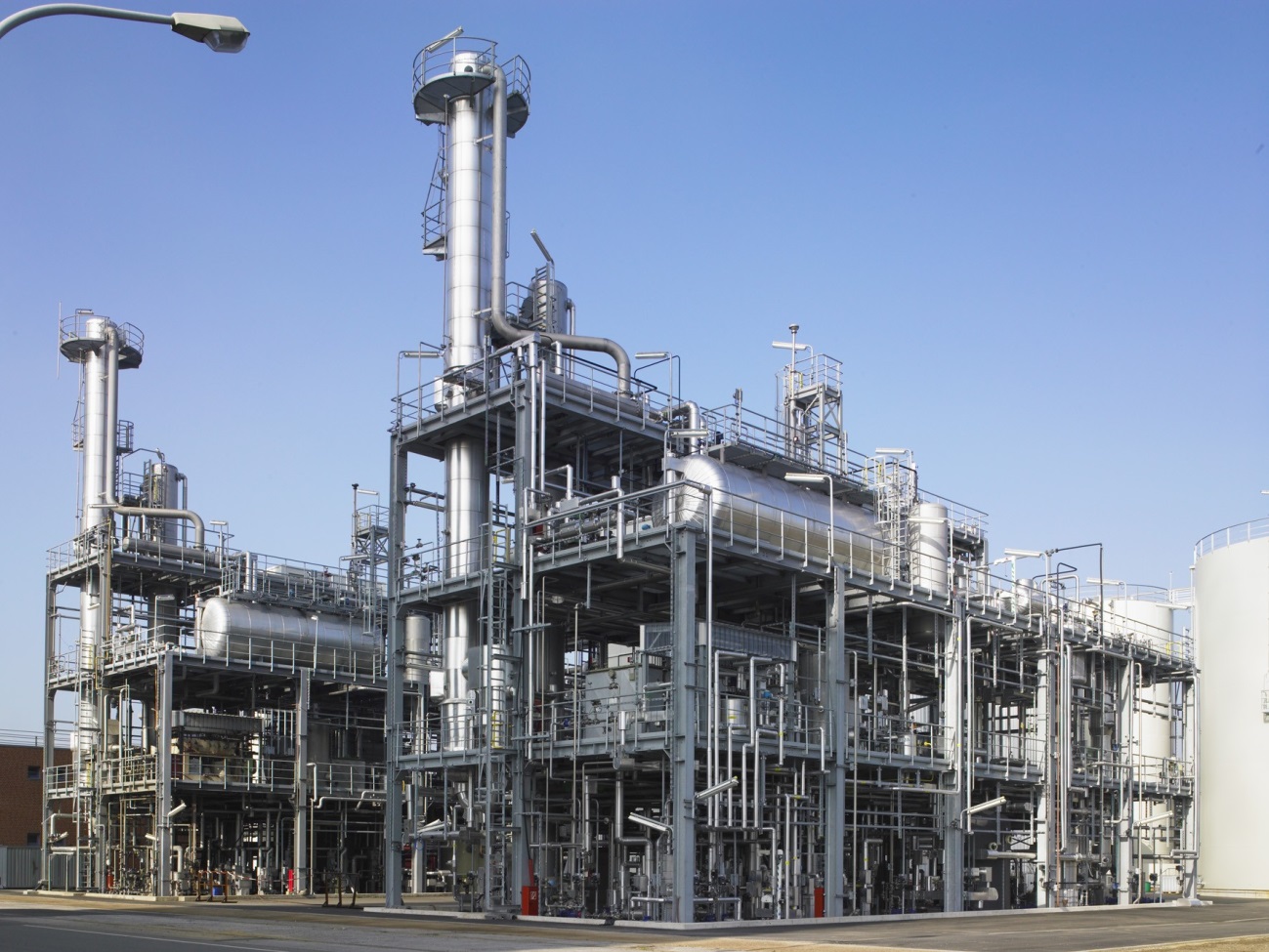