KCl Dechlorination with Sodium Bisulfite and Potash Lye Dosing Pumps
Potassium Chloride (KCl) - Dechlorination and pH Adjustment in Water Treatment
A report on the significance, procedures, and technical requirements
Location and Application:
The Lülsdorf chemical plant is a highly advanced production facility, encompassing a wide range of chemical processes, from chlorine electrolysis to the production of PVC and essential precursors for polyester. In this multifaceted environment, the quality and purity of chemicals are of paramount importance. This report sheds light on the pivotal role of process water, particularly dechlorination and pH adjustment, to ensure the smooth operation of production processes.
KCl Dechlorination:
In some industrial processes at the plant, particularly those involving chlorine electrolysis, water may be contaminated with chloride ions, often in the form of KCl. This chloride contamination can lead to various technical challenges, including corrosion and product quality issues. To neutralize chlorine, commonly used as a disinfectant, bisulfite is employed. It acts as a reducing agent, converting active chlorine into chloride ions:
Cl2 + H2O + SO32- → 2Cl- + 2H+ + SO42-
To optimize the process and ensure complete reactions, precise dosing of reagents is crucial.
2KOH + H2SO4 → K2SO4 + 2H2O
Technical Specifications:
For KCl dechlorination at the Lülsdorf chemical plant, pumps must meet the following parameters:
- Chemical resistance to sodium bisulfite 40% and potash lye (potassium hydroxide (KOH solution))
- Pulsation-free metering
- Flow rate between 300 and 500 l/h
- Differential pressure between 6.0 and 7.0 bar
- Magnetic-coupled rotary displacement pump, external gear pump
For this application, the customer has chosen the patented magnetic-coupled chemical gear pumps of the TEF-MAG® series by MARCH PUMPEN. All components in contact with the media are exclusively made of non-metallic materials to ensure optimal chemical resistance.
Pump and Materials:
TEF-MAG® 1500 – magnet drive chemical gear pump
- Pump Housing: Polypropylene
- O-Rings: EPDM
- Shafts: SSiC
- Gears: z1 PEEK-HPV / z2 PTFEC
- Bearings: Carbon Graphite
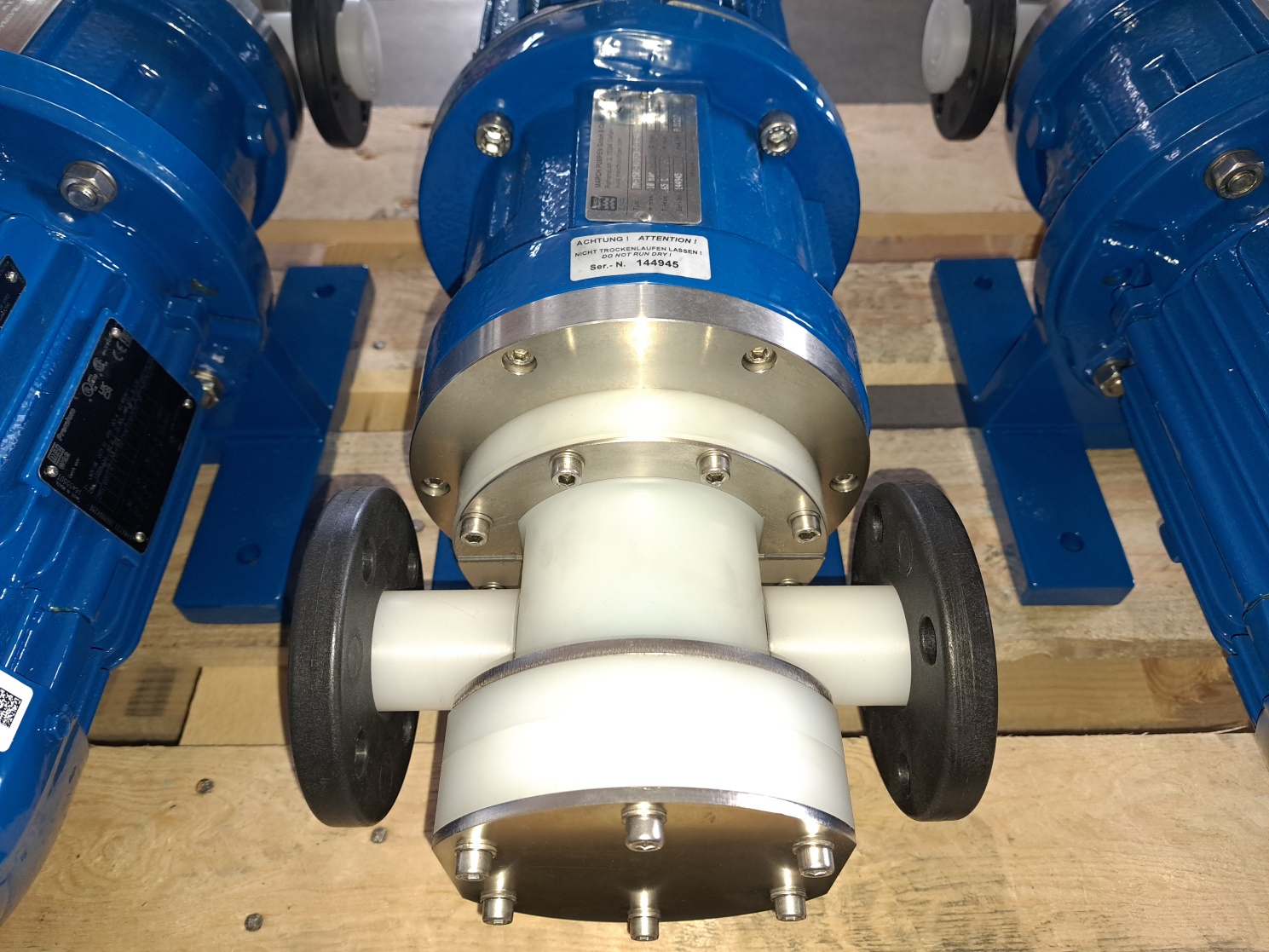