Pump for alkaline electrolysis
Alkaline electrolysis for the production of green hydrogen
TEF-MAG® - chemical resistant gear pumps made of completely non-metallic materials for hydrogen electrolysis to produce green hydrogen
On behalf of a Dortmund-based global market leader in the field of green hydrogen production, MARCH PUMPEN has custom configured a unique pump. The patented magnetically coupled gear pump TEF-MAG® forms the basis for this pump. The requirements for the new electrolysis process in a miniaturized "high pressure stack electrolyser" included a completely non-metallic pump in accordance with ATEX for 30% potassium hydroxide at operating temperatures of 70 to 90°C. Due to the need for a non-metallic material with a high pressure rating and ATEX compliance, a special material had to be found. In close cooperation with a material manufacturer, a suitable electrically conductive PEEK material was found whose high strength, continuous service temperature and chemical resistance make it possible to use plastics at high temperatures and pressures. All other wetted components of the pump are made of common and completely non-metallic as well as chemically resistant materials such as SiC, graphite and FFKM. The rotating displacement pumps of the TEF-MAG® series are external gear pumps and can deliver small volume flows at high differential pressures almost without pulsation.
Enquiry data / process data:
- Medium: KOH 30% (potassium hydroxide, potassium lye, caustic potash)
- Process temperature: 70°C … 90°C
- Inlet pressure: 16 bar
- Differential pressure: 9 bar
- Pump system pressure: 25 bar
- Volume flow: 20 l/h ... 250 l/h
- Hydrostatic pressure test at 37.5 bar
- ATEX II 2G (Zone 1)
- Operation on frequency converter
Pump type used / wetted materials:
TEF-MAG® 201
- Housing: PEEK (electrically conductive)
- Containment can: PEEK (electrically conductive) with external stainless steel sleeve for higher pressure ratings
- Shafts: SSiC
- Gears: PEEK-HPV
- Gear cage: PEEK-HPV
- Plain bearings: Graphite
- O-Rings: FFKM
- Internal magnet: PEEK (electrically conductive)
The process
Potassium hydroxide (KOH) electrolysis is a process used to extract hydrogen and oxygen from water. It is an electrochemical process in which a current is passed through an aqueous solution of potassium hydroxide, also known as an electrolyte solution.
During electrolysis with KOH, water is split into its components, hydrogen and oxygen. The process takes place in an electrolysis cell, which consists of a positively charged anode and a negatively charged cathode. Both electrodes are immersed in the electrolyte solution.
When a current flows through the anode, oxygen ions are formed, which settle on the anode. At the same time, a current flows through the cathode, forming hydrogen ions that settle on the cathode. The ion reactions at the anode and cathode release electrons that can flow through an external circuit and generate electricity.
The gas mixture of hydrogen and oxygen produced can be used to generate electricity or as a fuel. Electrolysis with KOH is an example of a sustainable and environmentally friendly way of generating energy, as the only by-product of electrolysis is water.
Electrolysis with KOH is often referred to as alkaline electrolysis and is one of several ways of splitting water into hydrogen and oxygen. However, alkaline electrolysis is less energy efficient compared to other processes such as PEM (Proton Exchange Membrane) electrolysis or SOEC (Solid Oxide Electrolysis Cell) electrolysis. Nevertheless, it is often the preferred method for large-scale industrial production of hydrogen due to its lower investment costs and simpler technology.
There are several factors that influence the efficiency of alkaline electrolysis, such as the concentration of the electrolyte solution, current density, temperature and pressure. A higher concentration of KOH in the electrolyte solution leads to higher conductivity, which reduces energy consumption. A higher current density increases the speed of the reactions at the electrode, but also the energy consumption. A higher temperature also accelerates the reaction rate, but at the same increases the wear of the electrodes and requires a higher cooling capacity. A higher pressure also increases the conductivity, but requires higher investment costs for the pressure vessels.
Overall, electrolysis with KOH is an important step towards sustainable and environmentally friendly energy production. Through the constant further development of the technology and the optimisation of the process parameters, alkaline electrolysis will continue to play an important role in the production of hydrogen in the future.
The efficiency of alkaline electrolysis depends on various factors, such as the composition of the electrolyte solution, the operating temperature and the electrode material used. As a rule, the efficiency of alkaline electrolysis is around 70 to 80 percent. This means that 70 to 80 percent of the electrical energy needed to carry out the electrolysis process is actually produced in the form of hydrogen and oxygen. The remaining energy is lost, for example in the form of heat.
Active research is being conducted on methods to improve the efficiency of alkaline electrolysis. An important focus is on reducing the cell voltage, which is currently one of the main factors for the low efficiency of alkaline electrolysis.
One approach to improving the efficiency is to develop improved electrode materials that are able to handle higher current densities and thus reduce the cell voltage. Another approach is to optimise the electrolyte solution to increase conductivity and lower cell voltage.
Other areas of research include the development of heat recovery systems to reduce the energy demand of the electrolysis process, and the integration of renewable energies such as solar and wind power to reduce CO2 emissions and the energy demand of electrolysis.
Why use non-metallic pump materials?
Using non-metallic materials for potassium hydroxide (KOH) electrolysis has several advantages.
Firstly, metallic materials can corrode and wear out at high temperatures and high concentrations of caustic potash, which can lead to failures and inefficiency. The use of non-metallic materials, especially plastics, can solve this problem as they are usually more chemically resistant to KOH and other electrolyte solutions.
Secondly, the use of non-metallic materials can reduce the risk of contamination from metal ions that may be released into the electrolyte solution and interfere with the electrochemical reactions or produce undesirable by-products.
Overall, the use of non-metallic materials can help to further improve the efficiency and reliability of electrolysis plants and make their operation more environmentally friendly.
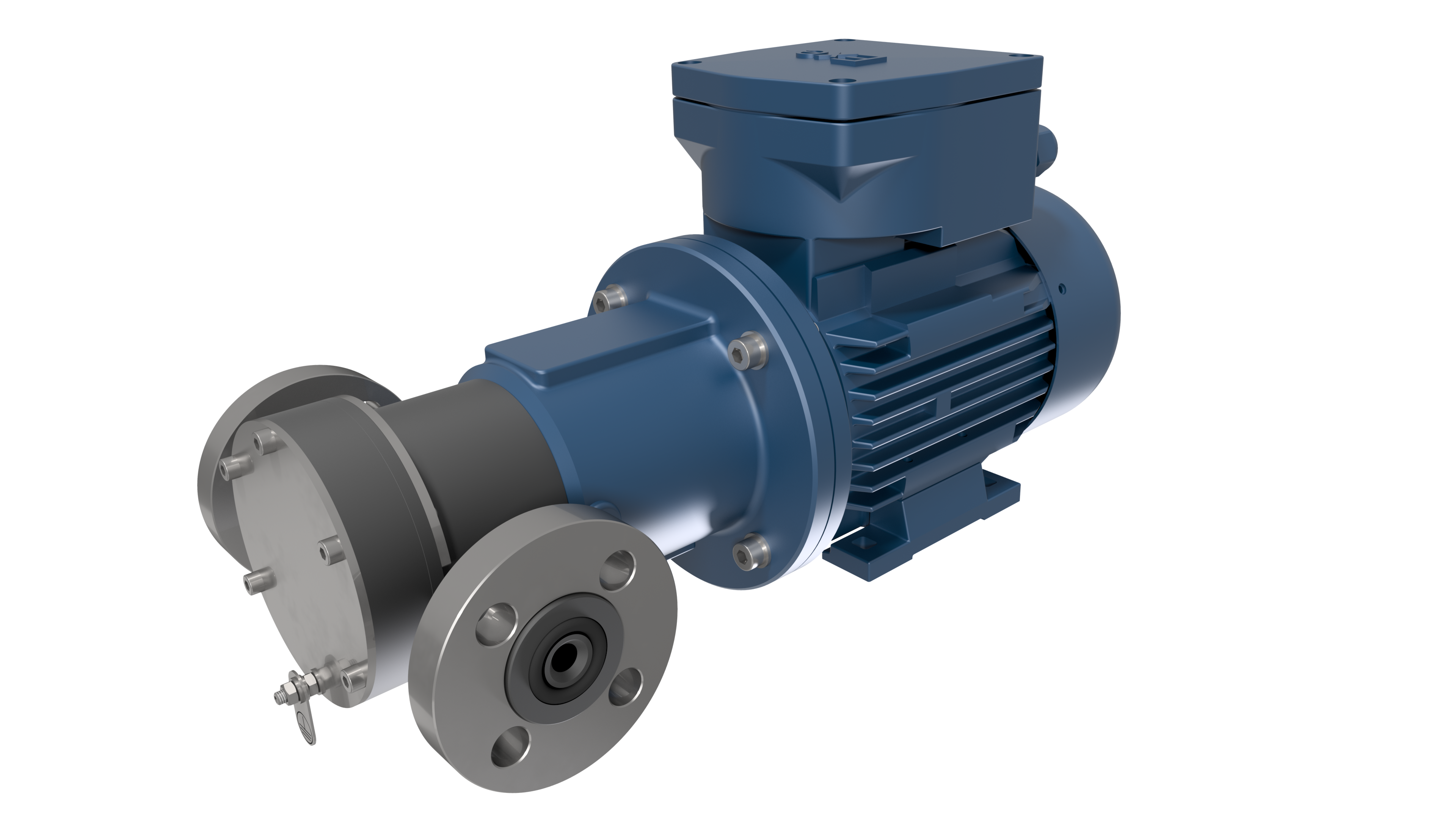