Case Studies
Successful Applications with MARCH PUMPEN
Explore a carefully curated selection of testimonials showcasing successful applications with MARCH PUMPEN. Our pumps have already proven their reliability in numerous projects. We are also happy to assess the feasibility for your specific application!
Contact us and speak to your representative.
Gear Pump made of PVC in Desalination Plants
Sodium Chloride Transfer with the TEF-MAG® Gear Pump made of PVC
A leading manufacturer of seawater desalination systems was looking for a reliable pumping solution for the transfer of highly concentrated sodium chloride (NaCl, brine, salt solution, saline water). Due to the high corrosion requirements and the need for a durable, low-maintenance system, the chemically resistant TEF-MAG® gear pump from MARCH PUMPEN was selected.
Optimization of production processes at NEW Biodiesel through the use of TEF-MAG® gear pumps
NEW - Natural Energy West GmbH is a company that specializes in the production of biodiesel and the processing of glycerine. NEW uses various pumping media and chemical reagents in its production processes. This case study focuses on the optimization of biodiesel production through the use of the chemical-resistant TEF-MAG® gear pump made entirely of non-metallic materials, as well as the transition from glycerine as a waste product to the main product.
Selective non-catalytic reduction of nitrogen oxides (SNCR process)
VANE-MAG® MPA - corrosion-resistant and magnetically-coupled rotary sliding vane pumps made of stainless steel for conveying ammonia water, technically leak-proof according to TA-Luft
The SNCR process is an established method for reducing nitrogen oxides (NOx) in emissions from industrial plants such as power plants, cement factories, or waste incinerators. It is a cost-effective way to reduce nitrogen oxide emissions and, in turn, air pollution and acid rain.
The SNCR process is based on the reduction of nitrogen oxides with ammonia (NH3) or urea (NH2CONH2) as reducing agents. The reduction takes place at high temperatures, typically between 850-1100 °C. The reducing agent is injected directly into the exhaust stream before the gases enter the flue gas cleaning system.
Wastewater neutralization
TEF-MAG® - chemical resistant gear pumps made of completely non-metallic materials for pumping acids and alkalis
Wastewater neutralization plants are equipment used to treat and neutralize wastewater before it is released into the environment. These plants are typically used in industrial plants, factories, hospitals, laboratories, and other facilities that generate large amounts of wastewater. Neutralizing wastewater is important to ensure that the wastewater is not harmful to the environment. Untreated wastewater can contain a variety of harmful substances such as heavy metals, organic chemicals, oils and greases, and pathogens and other pollutants. Wastewater neutralization uses a combination of chemical and physical processes to adjust the pH of the wastewater and remove pollutants. Various processes are used for this purpose, such as neutralization reactors, sedimentation plants, filtration devices, flocculation and other technologies ...
Lithium-ion battery recycling plant, battery recycling
TEF-MAG® - chemical-resistant gear pumps made entirely of non-metallic materials for battery recycling
MARCH-PUMPEN supplies global plant manufacturers for battery recycling plants. In total, processing capacities of more than 15,000 tons of electric car batteries can be returned to the value-added cycle. MARCH-PUMPEN thus actively supports sustainability in environmental protection by contributing to the avoidance of residual battery waste with the production and supply of the patented, chemical-resistant and magnetically coupled gear pumps made entirely of non-metallic materials of the TEF-MAG® series for dosing a wide variety of acids and other highly corrosive liquids.
In the process itself, the batteries are first mechanically treated to obtain the so-called "black mass", which consists of valuable raw materials such as lithium, cobalt, nickel and manganese. The black mass is then further processed hydrometallurgically using strong acids and other aggressive liquids. The metals are dissolved and separated in a special process.
Gear pump for HCl according to ATEX with FDA-compliant materials
TEF-MAG® - Leakage-free, magnetically-coupled, and chemically-resistant gear pumps made entirely from non-metallic materials in a block design. All components in contact with the media are made from FDA-compliant materials. Designed according to ATEX 2014/34/EU, Ex II2G, and DIN EN ISO 80079-36:2016, Ex h IIC Tx(65°C) Gb.
Hydrochloric acid is used as an auxiliary substance or reagent in various pharmaceutical processes. One example is the production of medications, where hydrochloric acid is used to adjust the pH value. It can also be used in the synthesis of active ingredients or in the cleaning of raw materials. Another example is the use of hydrochloric acid as a disinfectant in cleaning and sterilization processes in the pharmaceutical industry. In pharmaceutical production facilities for biotechnologically manufactured products such as food, feed, medicines, or other technical applications, the pipelines and product-contact components need to be cleaned at regular intervals. Typically, this is done using pumps specifically designed for this purpose, which need to handle cleaning agents, acids, and alkalis (for cleaning and neutralization). This process is called CIP (Cleaning In Place). Pharmaceutical plants often have potentially explosive atmospheres. Therefore, pumps are often required to meet challenging requirements, such as ensuring chemical resistance to the acids and alkalis used, ATEX compliance, and FDA conformity for the media-contact components to avoid contaminating the end products.
High Pressure Circulation Pump for Hot Water
MCA HT-HP - Corrosion-Resistant and Magnetically Coupled Chemical Standard Pumps for High Pressure and High Temperature Applications in Process Design
The MCA HT-HP series by MARCH PUMPEN offers corrosion-resistant magnetically-coupled chemical standard pumps for high-pressure and high-temperature applications in process design. These pumps have been specifically developed for use in gas turbine power plants and are employed in retrofitting as well as new projects to support the gas turbine system. The pumps must withstand high temperatures and pressures while ensuring high operational safety and extended service life.
Gas turbine systems require recirculation pumps to control the mass flow through the preheater under various load conditions and limit temperature gradients. These centrifugal pumps need to handle water at temperatures of up to 320°C and system pressures of up to 210 bar. ...
Production of biodiesel (fatty acid methyl ester)
VANE-MAG® MP/MPA - corrosion-resistant and magnetically coupled rotary vane pumps made of stainless steel or non-metallic materials for the conveying of biodiesel or catalysts.
TEF-MAG® - corrosion-resistant and magnetically coupled external gear pumps made of non-metallic materials for the conveying of biodiesel or catalysts.
MARCH dosing pumps of the TEF-MAG® and VANE-MAG® series can be found in biodiesel plants of AirLiquide, formerly Lurgi AG, and JJ-Lurgi Engineering worldwide. Biodiesel is produced from animal or vegetable fats and oils. The process of producing biodiesel is called transesterification, where the triglycerides in the fats and oils are converted into biodiesel (fatty acid alkyl esters) and glycerol by reacting with an alcohol and a catalyst. The most common alcohols used in transesterification are methanol or ethanol. The catalyst can be either a basic catalyst such as sodium or potassium hydroxide or an acidic catalyst such as hydrochloric or sulfuric acid.
Potassium Chloride (KCl) Dechlorination and pH Adjustment in Water Treatment
TEF-MAG® - Corrosion-Resistant and Magnetically Coupled Chemical Gear Pumps Made of Non-Metallic Materials for Conveying Acids and Alkalis
... For KCl dechlorination at the Lülsdorf chemical plant, pumps must meet the following parameters:
- Chemical resistance to 40% sodium bisulfite and potash lye (KOH solution)
- Pulsation-free metering of fluids
- Flow rate between 300 and 500 l/h
- Differential pressure between 6.0 and 7.0 bar
- Magnetically coupled rotary displacement pump, external gear pump
For this application, the customer has chosen the patented magnetically coupled TEF-MAG® Chemical Gear Pumps from MARCH PUMPEN. All components in contact with the media are exclusively made of non-metallic materials to ensure optimal chemical resistance.
Magnetically Coupled Centrifugal Pumps for Acids, Alkalis, and Solvents
Series M / EUROLINE - corrosion resistant and magnetically coupled centrifugal pumps made of stainless steel or non-metallic materials for acids, alkalis and solvents.
In modern industry, especially in the electroplating and semiconductor sectors, the use of high-quality pumps plays a pivotal role. Magnet-coupled chemical centrifugal pumps have become a preferred choice due to their reliability and efficiency. In this study, we highlight the advantages and applications of these pumps in both industries.
Denitrification with Methanol in Urban or Municipal Wastewater Treatment Plants
VANE-MAG® MPA - Corrosion-Resistant and Magnetically Coupled Stainless Steel Rotary Vane Pumps for Methanol Dosing
Denitrification is a process in wastewater treatment plants where nitrogen is removed from the wastewater. During this process, the nitrate content in the wastewater is reduced by converting nitrate into nitrogen gas. One method of carrying out denitrification in municipal wastewater treatment plants is by adding methanol as a carbon source.
In denitrification with methanol, methanol is added to the wastewater. The methanol molecules serve as a carbon source for the denitrifying bacteria present in the wastewater treatment process. These bacteria utilize methanol as an energy source and convert the nitrate in the wastewater into nitrogen gas. The resulting nitrogen gas is then released into the atmosphere, while the treated water undergoes further treatment to be returned to the natural water cycle.
The MPA rotary displacement pump from MARCH PUMPEN is highly suitable as a dosing pump for denitrification with methanol in urban or municipal wastewater treatment plants. This pump, made of corrosion-resistant stainless steel and the magnet drive, has proven its effectiveness in multiple applications.
Pumps for chemical filling in chemical storage facilities.
MCH series - Magnetically coupled chemical pump for industrial applications
When chemical resistance, robustness and durability are important! Then the non-metallic magnetic drive centrifugal chemical pump of the MCH series is the best choice!
As an innovative chemical company with numerous international locations, Zschimmer & Schwarz is a global player with customers all over the world.
In Lahnstein, the company operates a chemicals wholesale business where a wide variety of chemicals are delivered daily in tankers and then have to be filled into containers and other delivery vehicles.
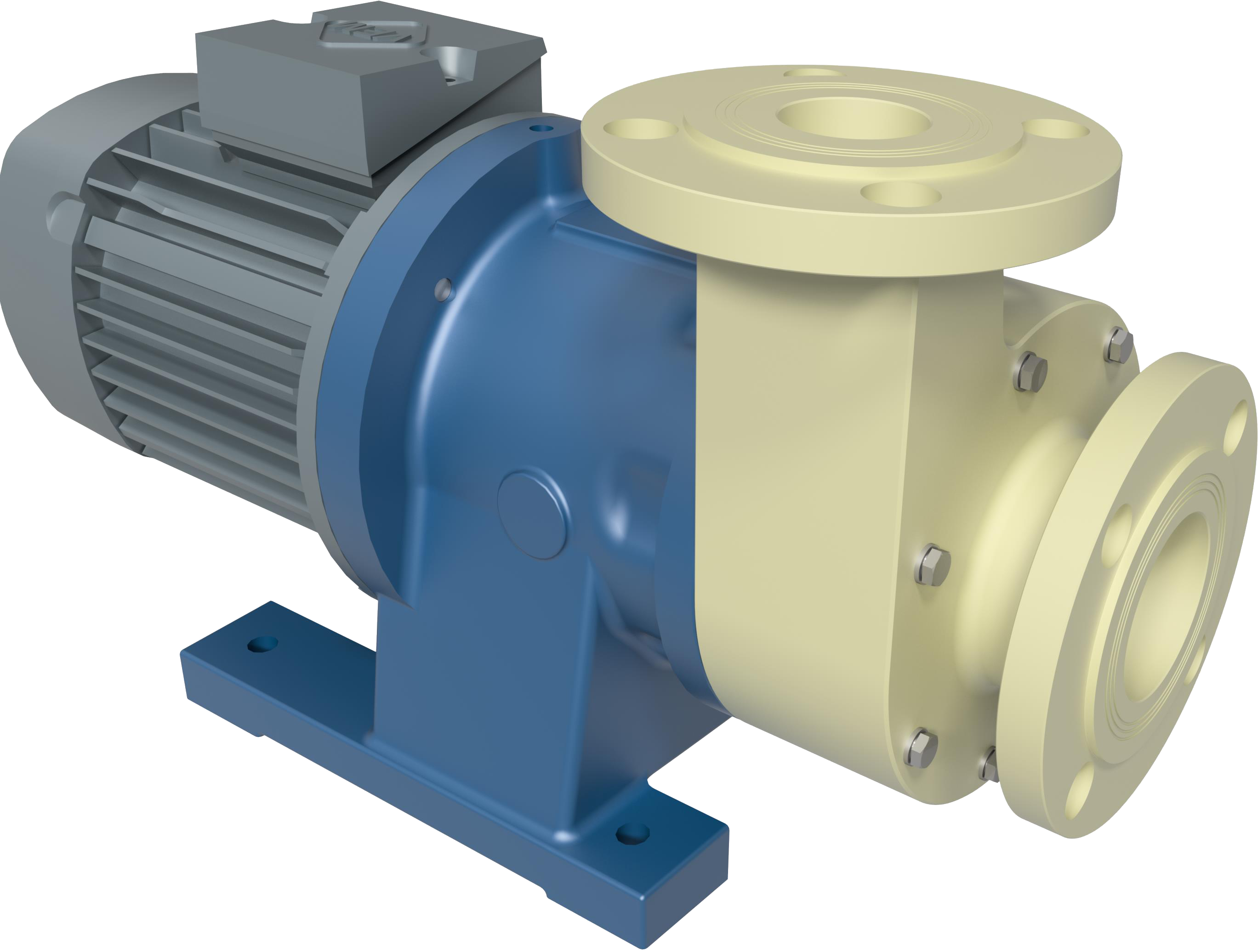
In 1994, the chemical warehouse, consisting of about 30 large tanks, was completely equipped with MARCH magnetic drive chemical pumps of the MCH series. The plant builder was the globally active KUSTAN GmbH from Gelsenkirchen.
Chemical-resistant gear pumps TEF-MAG® for high-pressure and high-temperature applications
In the realm of demanding technical applications, you encounter daily challenges that necessitate innovative solutions. This is where we excel: with the TEF-MAG® PEEK gear pumps from MARCH PUMPEN. When small quantities of highly corrosive liquids must be pumped in systems with substantial pressure losses, and high temperatures are required for the process, most pump systems fall short. MARCH PUMPENs patented TEF-MAG® external gear pump features not only a fully non-metallic hydraulic system but is also optimized for specialized applications.
Magnetically Coupled Rotary Vane Pumps: Ideal for pentane feed in the production of PU foam in metal composite elements and insulation panels.
VANE-MAG® MPA - mag drive rotary sliding vane pumps as pentane feed-pumps for PU foam production
Due to the flammability and high volatility of pentane, which has a boiling point of only about 36°C, special pump and system conditions are necessary. It is of paramount importance that the pumps operate without cavitation. Therefore, the NPSHA must be carefully determined and compared with the NPSHR. Usually, it should apply: NPSHA > NPSHR + 0.5m. It is also essential that no additional heat, especially at such a low boiling point, is added to the conveyed medium. Specific system conditions, such as low flow rates at high differential pressure, also limit the selection of suitable pump types.
Magnetically coupled rotary vane pumps ,also known as sliding vane pumps, of the VANE-MAG® MPA series offer ideal properties for this demanding process.
...
Alkaline electrolysis for the production of green hydrogen
TEF-MAG® - chemical resistant gear pumps made of completely non-metallic materials for hydrogen electrolysis to produce green hydrogen
On behalf of a Dortmund-based global market leader in the field of green hydrogen production, MARCH PUMPEN has custom configured a unique pump. The patented magnetically coupled gear pump TEF-MAG® forms the basis for this pump. The requirements for the new electrolysis process in a miniaturized "high pressure stack electrolyser" included a completely non-metallic pump in accordance with ATEX for 30% potassium hydroxide at operating temperatures of 70 to 90°C. Due to the need for a non-metallic material with a high pressure rating and ATEX compliance, a special material had to be found. In close cooperation with a material manufacturer, a suitable electrically conductive PEEK material was found whose high strength, continuous service temperature and chemical resistance make it possible to use plastics at high temperatures and pressures. All other wetted components of the pump are made of common and completely non-metallic as well as chemically resistant materials such as SiC, graphite and FFKM. The rotating displacement pumps of the TEF-MAG® series are external gear pumps and can deliver small volume flows at high differential pressures almost without pulsation.
Selective Catalytic Reduction of Nitrogen Oxides (SCR Process)
VANE-MAG® MPA - corrosion-resistant and magnetically coupled rotary vane pumps made of stainless steel for the conveying of urea for the reduction of nitrogen oxides
The SCR process
The Selective Catalytic Reduction (SCR) process is an exhaust aftertreatment technology primarily used for the reduction of nitrogen oxides (NOx) in the exhaust gases of combustion engines.
It was originally developed for diesel engines but is also applied in gas turbines and some stationary combustion plants.
The SCR process works by injecting a urea-based reducing agent, typically AdBlue or Diesel Exhaust Fluid (DEF), into the exhaust stream before a special catalyst.
Solvent dosing for the production of Polyvinylether
VANE-MAG® MPA - corrosion-resistant and magnetically-coupled rotary sliding vane pumps made of stainless steel for dosing solvents.
Polyvinyl ether is produced by the polymerization of vinyl monomers, in which a large number of vinyl groups are linked together to form a long polymer chain. There are various methods for producing polyvinyl ether, but the most common method is the radical polymerization of vinyl methyl ether (VME) or vinyl methoxy methyl ether (VMME).
The polymerization occurs in the presence of an initiator, which triggers the formation of radicals that then bind the monomers. The reaction can be carried out in an aqueous or organic solution or in a melt.
The steps for producing polyvinyl ether are as follows:
- Production of VME or VMME by reacting vinyl chloride with methanol or methoxy methanol.
- Polymerization of VME or VMME by radical polymerization in the presence of an initiator such as hydrogen peroxide or benzoyl peroxide.
- Separation of the polyvinyl ether by filtration, drying, or extraction.
TEF-MAG® Chemical-resistant gear pump made of non-metallic materials for the conveyance of sulfuric acid in the production of aramid fibers.
...The production process of aramid is demanding and requires precise sequences to achieve the special properties of these high-performance fibers. Sulfuric acid (H2SO4) plays a central role, especially in the wet spinning process for the production of aramid fibers.
In the production of aramid fibers, especially in the well-known process for producing poly(p-phenylene terephthalamide), sulfuric acid acts as a spinning fluid. It serves as a solvent for the aromatic polyamide used to produce aramid fibers. The polymer is dissolved in concentrated sulfuric acid to obtain a spinneret solution. This solution is pressed through fine nozzles to create threads. These threads are introduced into a coagulation bath, typically a diluted sulfuric acid solution, where the polymer is precipitated, and fiber formation starts. The high sulfuric acid concentration allows the alignment of the polymer chains in the solution before fiber formation an essential step to achieve the impressive tensile strength properties of aramid fibers....
MARCH PUMPEN VANE-MAG® series
The MARCH PUMPEN VANE-MAG® series are magnetically coupled rotary sliding vane pumps made of stainless steel or non-metallic materials, which are designed for the most demanding industrial applications.
MARCH VANE-MAG® pumps are self-priming, dry-running positive displacement pumps, ideal for applications with low flow rates at high discharge pressure. They are ideal for metering low-viscosity and non-lubricating liquids.